Slurry pumps used in operations such as coal preparation plants and other wet-plant operations must endure harsh conditions. Efforts to prevent the entry of water and solid contaminants to pump barrels will extend bearing service lives.
The use of automatic lubrication systems to provide a regular purge of fresh grease through the labyrinth seals of pump barrels is a common and proven method of preventing contaminant entry. As the harshness of the operating conditions increases, so too does the importance of the automatic purging.
Pumps which are subjected to regular wash down or which have water impingement to the wet-end labyrinth demand higher labyrinth purge rates.
In addition to seal purging, automatic systems can also be implemented for bearing re-lubrication in order to provide precise and controlled grease delivery, thereby avoiding grease starvation and over lubrication.
Challenges
Slurry pumps in particular are often operated under very challenging operating conditions with heavy contamination from water and slurry. Because of this extra care must be taken to prevent the entry of contaminants to the pump bearing.
For pumps which employ labyrinth type shaft seals the optimal method of preventing contaminant entry is to inject small volumes of grease at short time intervals. This effectively achieves a constant purge of clean grease. The flow of clean grease from the labyrinth seal to atmosphere prevents the inward entry of liquid and solid contaminants. The use of single point lubricators* to achieve such a purge of grease is proven and commonly accepted maintenance strategy.
For pumps which operate relatively high speeds, and potentially at elevated temperatures, also present challenges for bearing relubrication. Care must be taken to constantly avoid the development of lubricant starvation, yet over-lubrication must also be avoided. Consequently, single point lubricators* are often employed for bearing relubrication in order to achieve an equilibrium of full lubrication, avoiding lubricant starvation and over-lubrication.
* Also commonly referred to as autolubes or SPLs
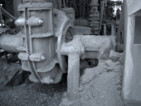
Dirt, water or other contaminants must not enter the bearing points
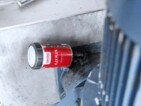
Lubrication while the machine is in operation must be ensured
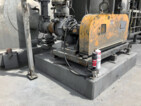
Workplace safety must be ensured
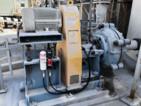
Operation in potentially explosive areas
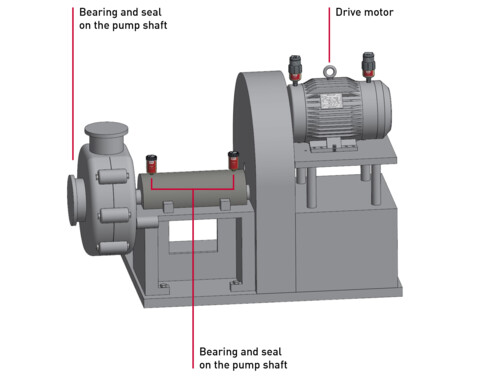
Lubrication points
Lubrication points (roller bearings) are located on the drive shaft between drive motor and pump body or in the pump housing.
Lubrication of gland seal and labyrinth seal prevents the ingress of dirt and / or pumped media into the bearing. Seals of bearings and bearing housings must be permanently supplied with the specified amount of the right lubricant.
Solutions
Mount a perma lubrication system at the lubrication point. Depending on the conditions prevailing at the lubrication point, the perma lubrication system can either be mounted directly or remotely.
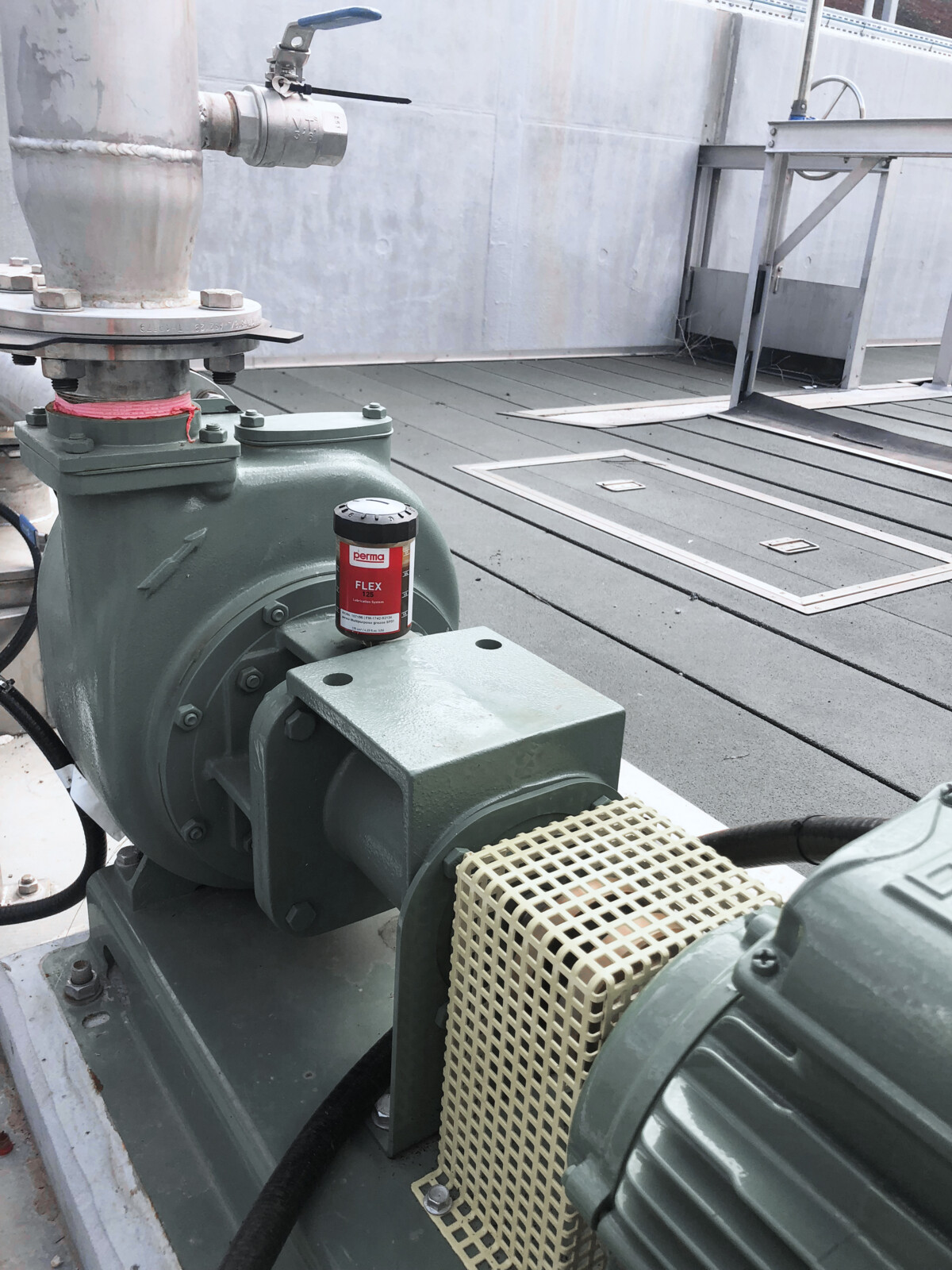
- Easy, quick mounting
- For lubrication points with little vibration / shocks
- For easy-to-reach, safe lubrication points
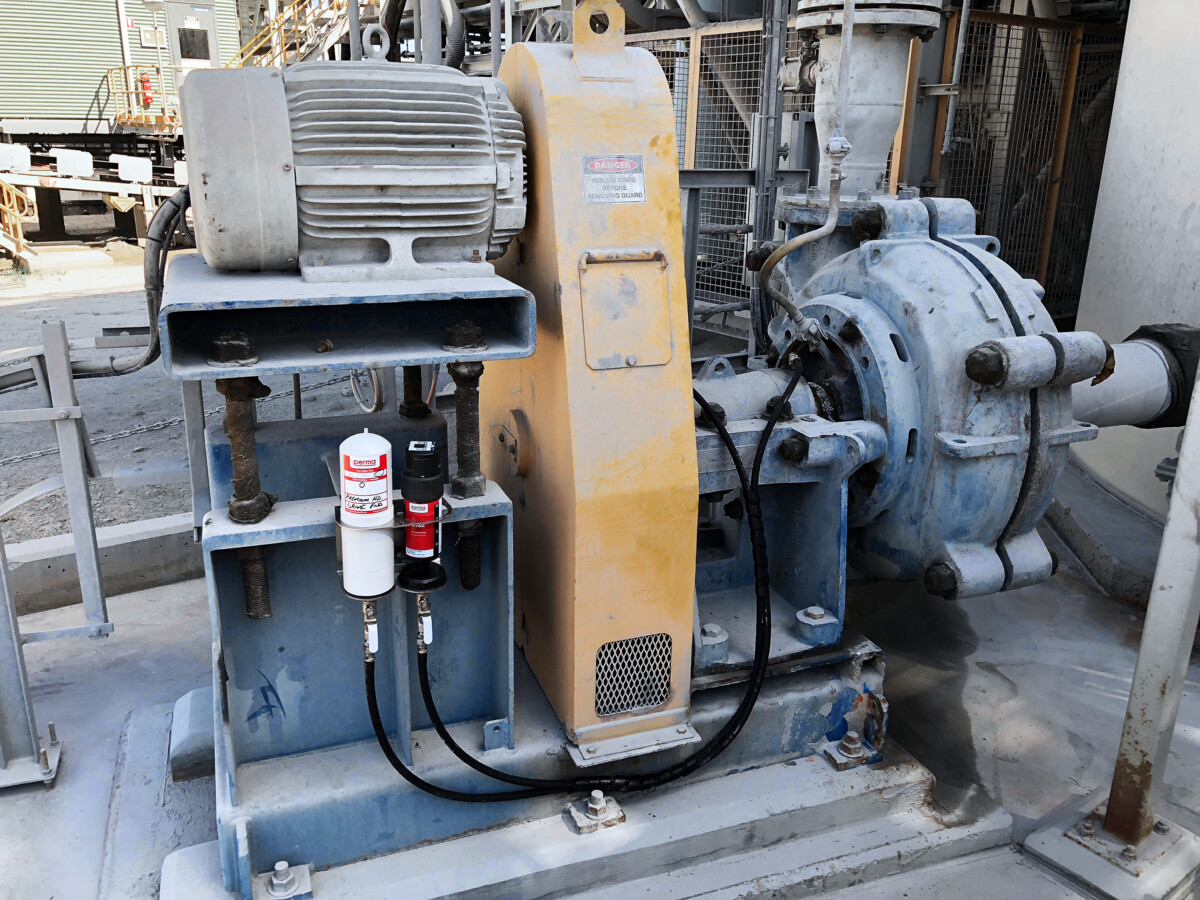
- For lubrication points with strong vibration / shocks (isolation of lubrication system)
- For lubrication points which are unsafe to access: Mounting in safe areas
- For hard-to-reach lubrication points
Any more questions?
Simply contact us by phone or email for an individual consultation on pumps.
Advantages of automatic lubrication
Work place safety
Work place safety can be improved via automating a manual work task
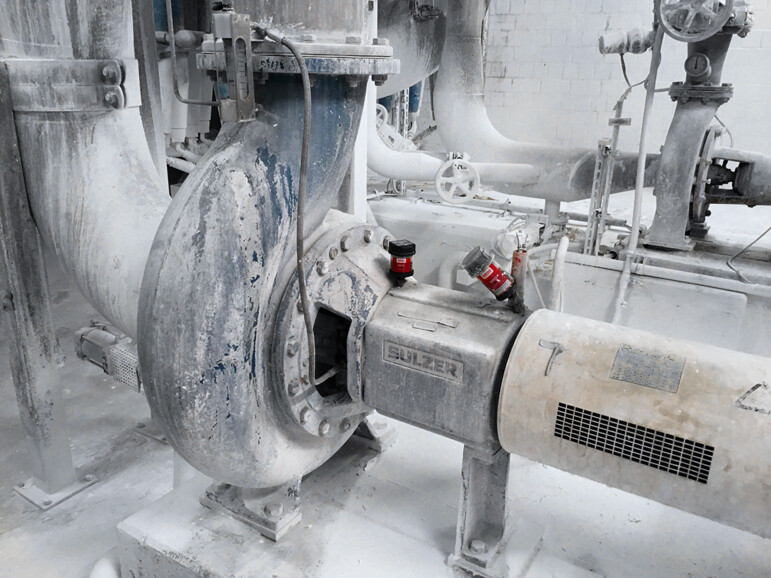
Extended service life
Bearing service life is extended by avoiding lubricant starvation and over-lubrication
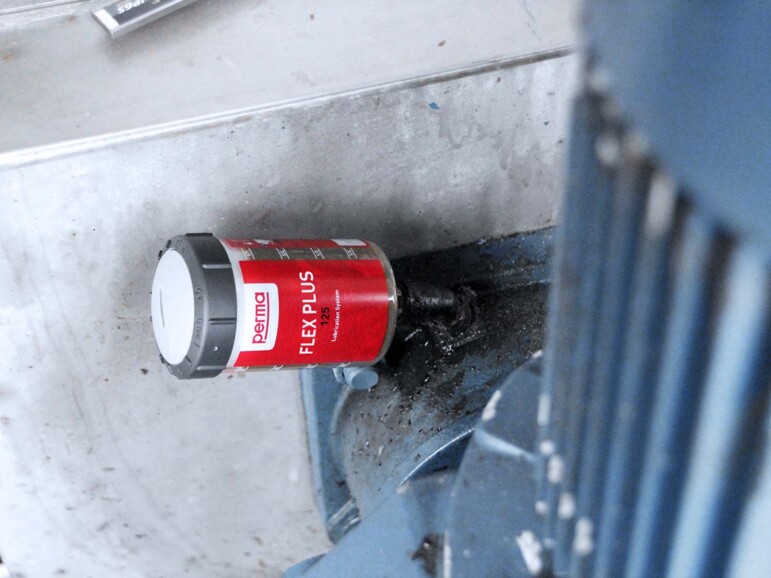
Constant purge
Frequent additions of small quantities of grease provides a constant purge of grease through shaft seals to prevent contaminant entry

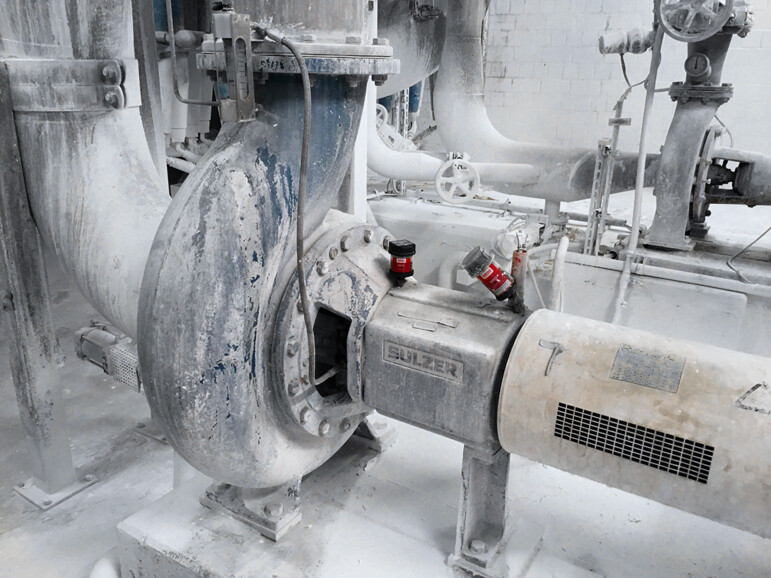
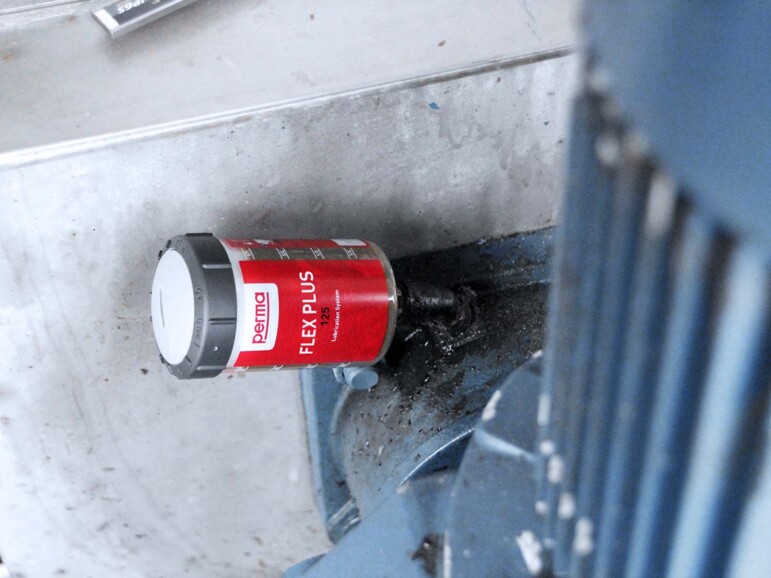
